Hiring a trusted service provider for stretch wrap machine repair is a wise business decision.
Hiring a trusted service provider for stretch wrap machine repair is a wise business decision.
Blog Article
Comprehending the Significance of Timely Stretch Wrap Device Repair Work Solutions
When it comes to extend cover equipments, prompt repair work can make all the distinction. What elements should you think about to assure your machines stay in top shape?
The Duty of Stretch Wrap Machines in Modern Manufacturing
Stretch cover devices play an essential function in modern manufacturing by ensuring that items are firmly packaged for transportation and storage space. You depend on these makers to give security and defense, stopping damage during transit. When you make use of stretch cover, you decrease the threat of products moving or getting crushed, which can result in costly losses.
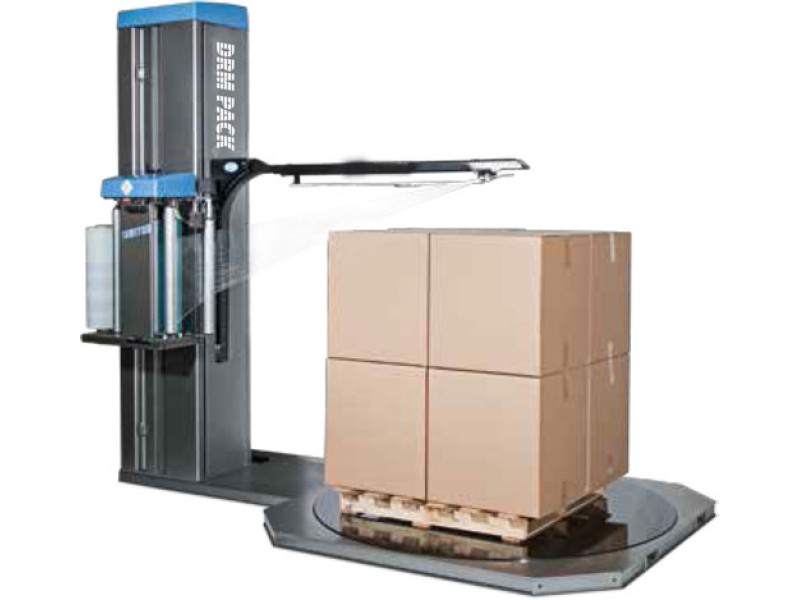
Additionally, making use of stretch wrap equipments can enhance your overall supply chain performance. By streamlining the product packaging procedure, you decrease labor prices and accelerate distribution times, ensuring that your customers obtain their products without delay. In today's hectic market, this benefit is vital.
Usual Issues That Cause Device Downtime
When your stretch wrap machine experiences downtime, it can commonly be traced back to mechanical failures or operator mistakes. Recognizing these typical concerns can assist you prevent costly disturbances. By resolving these factors, you can maintain your procedures running efficiently.
Mechanical Failings and Break Downs
When components put on down or break, your stretch cover equipment may stop unexpectedly, influencing efficiency. Furthermore, electrical failures can trigger malfunctions in the machine's control system, creating more delays. By prioritizing timely fixings, you're not just reducing downtime however also expanding the life expectancy of your device.
Operator Errors and Oversights
While drivers play an essential function in the smooth performance of your stretch cover machine, their errors and oversights can bring about substantial downtime. Usual problems like incorrect loading, wrong setups, and failure to monitor wrap stress can create delays and product damage. For instance, if an operator forgets to look for worn-out movie, it can result in irregular covering and boosted waste. Additionally, miscommunication throughout shifts can result in important modifications being neglected. It is essential to give comprehensive training and normal refresher courses to decrease these errors. Urging a culture of responsibility and vigilance amongst your group can significantly decrease downtime. Ultimately, purchasing operator training repays by boosting effectiveness and prolonging your maker's lifespan.
The Financial Influence of Postponed Repair Services
Postponing fixings on your stretch cover equipment can result in considerable monetary repercussions that ripple through your entire procedure. When your maker breaks down, efficiency plummets. Each hour of downtime can cost your business not just in lost output, yet additionally in labor costs as workers stand idle. You might additionally deal with boosted material wastage as a result of improper covering, leading to greater prices for packaging materials.
Additionally, extended hold-ups can escalate small issues right into significant problems, needing more considerable repairs or even total replacement of the maker. Inevitably, timely repair work are important to maintaining your bottom line and guaranteeing smooth procedures.
Advantages of Proactive Maintenance Programs
Prompt repairs can save you from expensive downtime, however executing a positive maintenance program takes it a step further. This not just keeps your stretch cover maker running smoothly yet likewise expands its life expectancy.
Moreover, an aggressive technique improves productivity. With fewer disruptions, your workforce can concentrate on their tasks without the tension of unexpected maker failings. Plus, you'll likely save money on repair expenses, as small problems are typically much less costly to repair than considerable repair services. Finally, preserving peak efficiency can boost the high quality of your covered products, guaranteeing client complete satisfaction. In the long run, a proactive maintenance program is an investment that pays off via boosted reliability and cost financial savings.
Identifying Indications That Your Equipment Needs Repair
As you run your stretch wrap equipment, it is crucial to remain vigilant for indicators that show it may require repair service. Among the very first points to seek is uncommon noise. If you hear grinding, squeaking, or any type of other strange sounds, it can signify an underlying problem. In addition, look for inconsistent wrapping. If the movie isn't stuck effectively or you notice unequal stress, your equipment could be malfunctioning.
One more indicator is a rise in downtime. If your equipment frequently stops or requires changes, it is time to investigate. Keep an eye on the equipment's speed; if it's slower than usual, something might be incorrect. Lastly, any noticeable damages like frayed wires or leaks should not be neglected. Without delay resolving these indicators can avoid more considerable problems down the line, ensuring your operations run efficiently.
Choosing the Right Fixing Service for Your Demands
How do you select the appropriate repair service for your stretch wrap device? Look for technicians who specialize in stretch wrap makers and have a tried and tested track record.
Following, review their response time. A dependable solution should provide timely support, as maker downtime can be pricey. It's also important to understand if they supply emergency repair services.
Do not neglect to inquire about guarantees on repairs and parts. A credible solution guarantees their job, offering you satisfaction.
Last but not least, contrast rates yet stay clear of picking exclusively based on cost. In some cases, the most affordable option may result in substandard service. By considering these variables, you'll discover a repair work solution that fulfills your requirements and maintains your stretch cover equipment running efficiently.
Strategies for Reducing Stretch Cover Maker Downtime
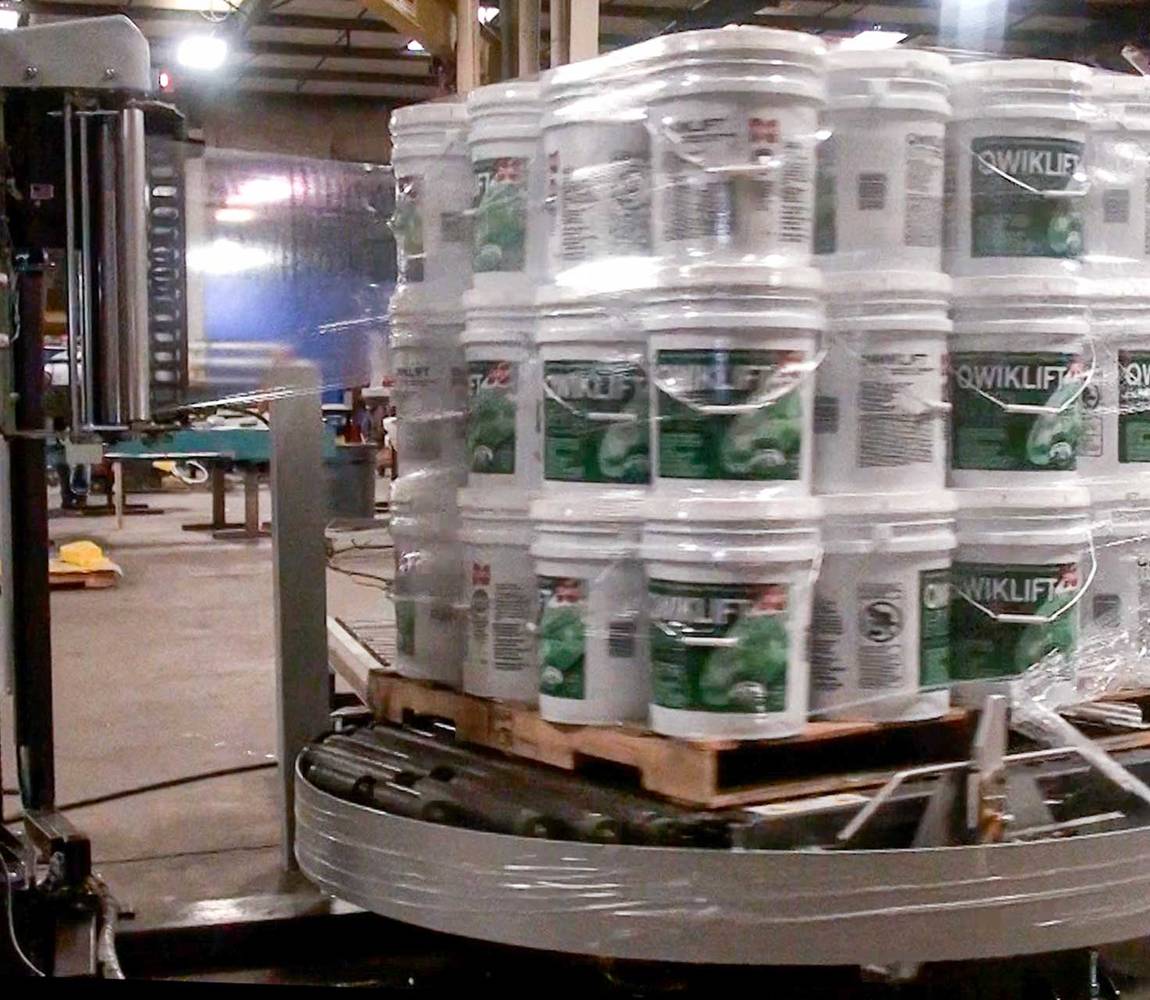
Educating your operators is an additional important strategy. Outfit them with the expertise to determine and deal with small problems prior to they result in considerable break downs. Motivate them to maintain a log of any type of irregularities, which helps in identifying problems faster.
Furthermore, maintaining an inventory of crucial spare components can substantially lower downtime. When something breaks, having the appropriate parts accessible means you will not need to await deliveries.
Lastly, take into consideration buying real-time monitoring systems. These systems can notify you to efficiency adjustments, site web allowing for instant intervention. By carrying out these methods, you'll keep your stretch wrap device running smoothly and effectively.
Often Asked Questions
Just How Commonly Should Stretch Cover Machines Be Serviced?
You must service stretch cover machines consistently, preferably every 6 months. However, if you see any kind of efficiency concerns or uncommon noises, do not wait-- schedule maintenance promptly to stop pricey failures and guarantee peak effectiveness.
What Are the Regular Expenses Connected With Stretch Wrap Device Repair Works?
Typical prices for stretch wrap equipment repair services vary, yet you may expect to spend in between $200 to $1,500 relying on the issue. Regular upkeep can help minimize these prices and prolong your equipment's life-span.
Can I Do Basic Maintenance on My Stretch Wrap Machine?
Yes, you can perform standard maintenance on your stretch wrap machine. Routinely inspect for wear and tear, cleanse the components, and warranty correct lubrication. Keeping it in excellent shape can prolong its life expectancy and boost performance.
Exactly how Do I Know if a Repair Solution Is Respectable?
To locate a respectable fixing solution, inspect on-line reviews, ask for referrals, and validate certifications. A trusted service will supply clear estimates, service warranty options, and punctual interaction, guaranteeing you feel great in their expertise.
What Should I Do in Instance of an Emergency Situation Equipment Failure?
In case of an emergency situation equipment malfunction, you must right away quit operations, analyze the concern, and contact your repair work solution. Maintain vital get in touch with numbers website link convenient, and document the issue for efficient repairing when help shows up.
Final thought
To summarize, recognizing the value of timely stretch wrap device repair work can substantially improve your procedures. Bear in mind to remain vigilant for signs of wear and select a dependable repair service to maintain your devices running smoothly.
Report this page